What Is Supply Chain Management?
Supply Chain Management or SCM is the coordinated end-to-end management of the entire production flow of goods and services, from the sourcing of raw materials to the delivery of the final product to the consumer. It refers to all the activities that create finished goods from raw materials and deliver them to the customer. That means, SCM is a comprehensive process that involves planning, implementing, and storing goods and services from the point of origin to the end user. It includes activities like sourcing, production, warehousing, shipping, and distribution. SCM’s goal is to improve efficiency, quality, and customer satisfaction.
Supply Chain Management also focuses on improving supply chain processes, which can benefit both customers and business partners. The goal of SCM is to optimize efficiency and effectiveness, ensuring that products are produced and distributed in the right quantities, to the right locations, and at the right time, all while minimizing costs and then meeting customer requirements to help businesses achieve a competitive advantage and enhance overall performance.
What Is Supply Chain?
To understand Supply Chain Management, we need to understand its base – the Supply Chain, which is the backbone of end-to-end process of the production flow of goods and services.
A Supply Chain is a network of people, organizations, resources, tools, and technology that work together or in sync to create and sell a product or service, from the place of its production to the place of its consumption. In simple words, all the components that take part in completing a customer’s request, directly or indirectly, are part of the complete end to end supply chain. These includes, but not limited to, the following main participants of the supply chain:
- The Customer: Who consumes and demands any product or service.
- The Retailer and Service Providers: Who completes customer’s demand on products and services.
- The Manufacturer: Who manufactures or converts raw materials into valuable products.
- The Supplier: Who supplies the raw materials to the manufacturer.
- The Transporter: Who moves raw materials from suppliers to the manufacturers or finished products to the retailers.
- The Warehouse: Where raw materials or finished products are temporarily and safely stored.
- The Planner: Who plans and manages all these processes from initiation to the execution.
Since supply chain is a large network of people, organizations, resources, tools, and technology, so it generally occurs across different business organizations. However, it can occur within an organisation as well.
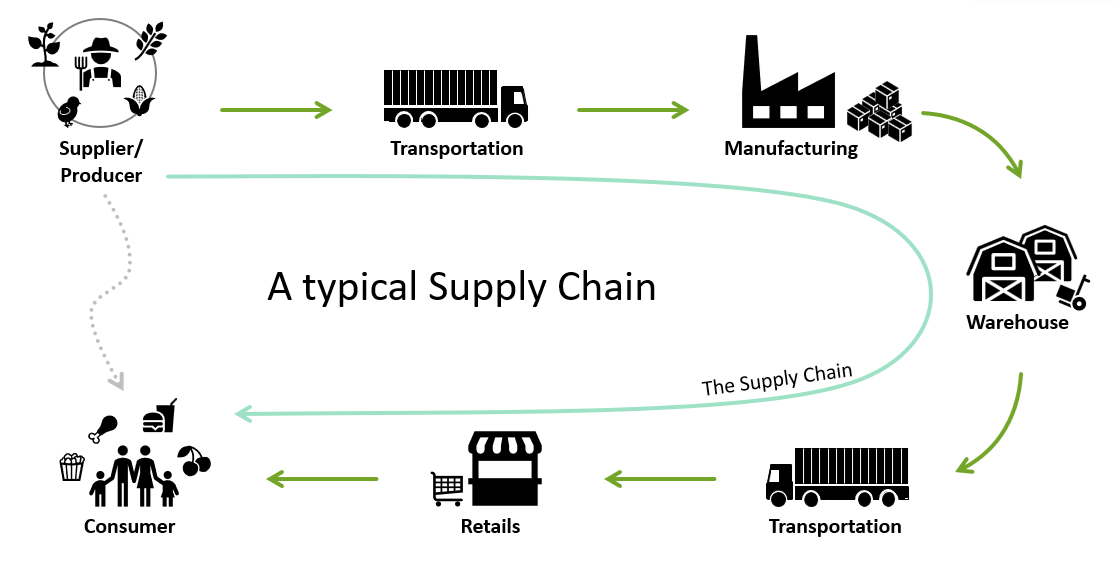
What are the Components of Supply Chain Management?
Supply Chain Management involves overseeing an often-vast network of stakeholders like, sub-suppliers (like raw materials providers), suppliers, manufacturers, logistics partners, wholesale distributors, retailers and end users. These participants are involved in various activities of planning and management to run the production flow of goods or services smoothly. The activities basically form the major components of the SCM domain, which includes:
- Planning: Forecasting demand, arranging production and managing inventory levels.
- Sourcing: Identifying and assessing potential suppliers that offer the best value.
- Procurement: Acquiring the best identified source and paying for goods and services.
- Production or Manufacturing: The process of converting raw materials into valuable products.
- Logistics: The process of planning and executing the efficient transportation and storage of products.
- Delivering: The process of distributing products from storage to the location of the final customer.
- Returning: The process of customers sending back products to distributer after purchasing them.
The above listed activities of Supply Chain Management ultimately lead to various businesses like new product development, marketing, operations, distribution, finance, and customer services.
What is Logistics in Supply Chain Management?
Supply Chain Management is a broader system of processes that includes Logistics, which is basically a part of the core supply chain that focuses on the movement, storage, and flow of goods, services, and information. In short, logistics activities are part of the broader Supply Chain Management system and include transportation, warehousing, packaging, and order fulfilment.
Logistics involves planning and executing the storage and movement of goods between different points in the supply chain. Logistics coordinates facilities, people, equipment and other resources to ensure products move when they’re supposed to and there is space for them at the next stop. The main objective of logistics is to deliver the right product at the right time through activities such as demand planning, transportation and fleet management, inventory management, material handling and order fulfilment.
To summarise, Supply Chain Management involves comprehensive coordination between various partners that have a role in the supply chain to ensure a smooth and efficient flow of goods and services in the network, whereas logistics focuses on the actual movement and storage of items in the supply chain.
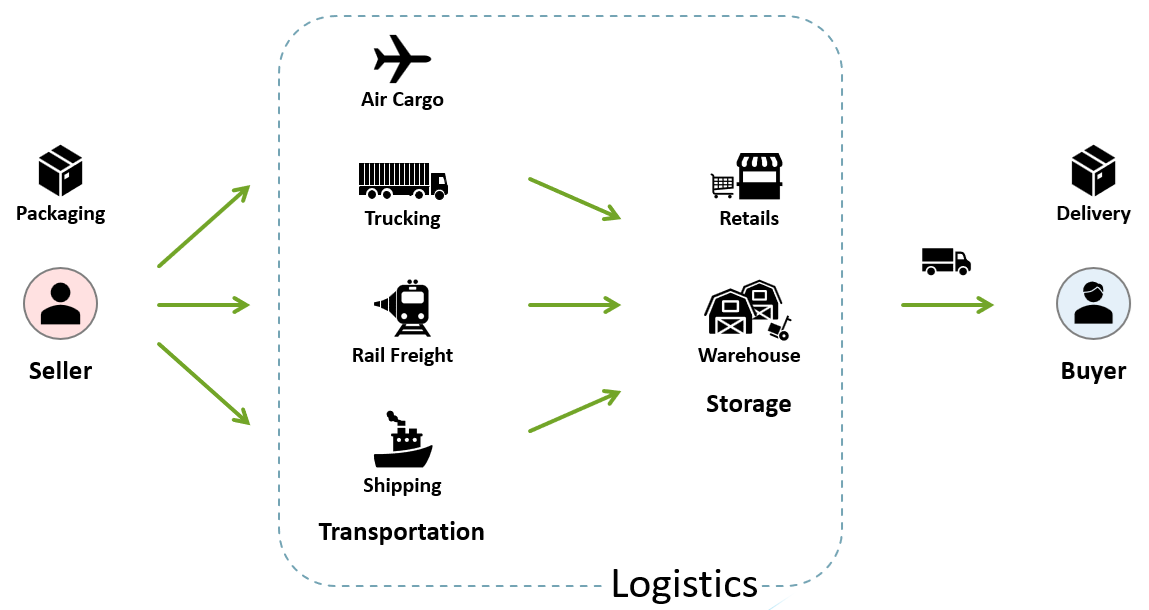
What is Logistics Management in SCM?
Logistics Management is the process of planning, implementing, and controlling the movement of goods, services, and information between the point of origin and the point of consumption. Logistics management is the core business of supply chain management that drives cash flow. Six major benefits of effective logistics management are as follows:
- Visibility: Enables businesses with greater visibility into the supply chain to better control costs, tease out efficiencies, spot supply chain problems, conduct demand planning and gain insights into opportunities.
- Reduced overhead: Enables companies to reduce overhead costs in areas from cutting shipping costs to shrinking how much warehouse space they need by proactively controlling inventory levels.
- Preventing loss: Provides true inventory accounting to know exactly how much stock is in hand at any given time. Helps track movement and current location so that stock are not misplaced or diverted without notice. Prevents spoilage and damage by ensuring optimal storage and transport conditions.
- Improved customer experience: Helps to win repeat sales by delivering orders accurately and quickly, improving customer experience, which in turn increase brand loyalty and future sales.
- Support expansion: Helps forecasting demand by realistically calculating inventory needs and ordering, transporting and stocking accordingly, thereby help companies scale to fulfil more customer orders on time.
- Competitive edge: Helps delivering orders correctly and on time, which in turn help a company acquire new buyers. Also, helps a company consistently deliver on promises and sharpen its competitive edge.
A company can only optimize and continuously refine SCM when it has visibility across its supply chain. This visibility enables companies to track goods and services as they move through each stage of the supply chain, which makes it much easier to see if everything is running as planned. It also gives decision-makers more time to respond to disruptions or other roadblocks.
The relationships between these various stakeholders in the supply chain vary. They can be vertical, such as between parts and materials suppliers, manufacturers and retailers, or horizontal, where a company merges with or acquires a similar business that operates at the same stage of the supply chain.
What is Supply Chain Visibility?
Supply Chain Visibility (SCV) is the ability to track individual components, sub-assemblies and final products as they travel from supplier to manufacturer to consumer. The broad goal of Supply Chain Visibility is to collect better information about supply chain operations, improve efficiency, reduce risk, boost customer satisfaction and increase profits. SCV provides actual data about logistics and other aspects of supply chain that helps to manoeuvre around inventory shortages, avoid bottlenecks, meet compliance directives and track products through to delivery.
Supply Chain Visibility plays a pivotal role in Supply Chain Management by providing real-time data and insights across the entire supply chain, from raw materials to the end customer. This enhanced visibility enables companies to track and trace products at every stage, ensuring transparency and accountability. By having a clear view of inventory levels, shipment statuses, and potential disruptions, businesses can make informed decisions, reduce risks, and optimize their operations. SCV also fosters better collaboration among supply chain partners, leading to improved efficiency, reduced costs, and a more responsive and resilient supply chain. In essence, SCV transforms supply chain operations from reactive to proactive, allowing companies to anticipate and address issues before they escalate, ultimately enhancing overall performance and customer satisfaction.
Types of Supply Chain Visibility
Most of the Supply Chain Management software applications are built to provide the Supply Chain Visibility. The primary goal of these applications is to offer real-time data and insights throughout the supply chain, enabling better decision-making, improving efficiency, and ensuring transparency. By providing SCV, these software solutions help businesses track and manage inventory, monitor shipment statuses, identify potential disruptions, and collaborate more effectively with supply chain partners. In essence, SCV is a critical feature of SCM software, driving overall supply chain performance and resilience. When deciding how and where to gain greater insights into the supply chain, the following types of Supply Chain Visibility should be considered:
- Cargo Location: Provides real-time visibility of the location and status of shipment to know the exact whereabouts.
- Rates: Provides visibility into the costs related to the transportation of cargo helps understand how much companies are spending moving, shipping and delivering freight, which is necessary to conduct cost-benefit analyses.
- Auditing Records: Provides visibility into past transactions helps to fully inspect, review and validate past completed orders. Greater transparency within auditing makes complying with regulations much easier.
- Supply Chain Activities: Provide details on the supply chain activities like tracking quotes, order receipts, bills of lading, proof of delivery etc.
Process View of Supply Chain
A supply chain includes a sequence of processes and flows that work together or in sync to fulfil the customer demands. The process view of supply chain is a way to understand and manage the various processes involved in a supply chain. It includes two main perspectives: The Cycle View and the Push/Pull View.
Cycle View: The Cycle View breaks down the supply chain into a series of cycles, each performed at the interface between two successive stages of the supply chain. The main cycles are:
- Customer Order Cycle: Involves processes directly related to receiving and filling customer orders.
- Replenishment Cycle: Involves processes related to restocking inventory.
- Manufacturing Cycle: Involves processes related to producing goods.
- Procurement Cycle: Involves processes related to acquiring raw materials and components.
Push/Pull View: The Push/Pull View categorizes supply chain processes based on whether they are initiated in response to a customer order (pull) or in anticipation of a customer order (push).
- Push Processes: These are initiated based on forecasts and are performed in anticipation of customer orders.
- Pull Processes: These are initiated in response to actual customer orders.
The boundary between push and pull processes is crucial for strategic decisions in supply chain management.
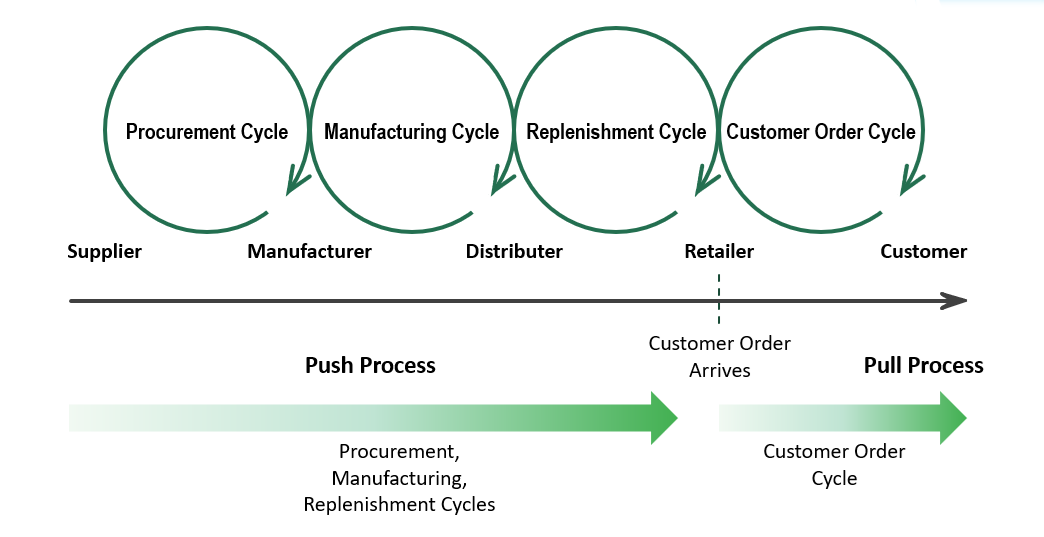
The Bullwhip Effect
The bullwhip effect in supply chain management refers to the phenomenon where small fluctuations in demand at the customer/retail level can cause progressively larger fluctuations in demand at the wholesale, distributor, manufacturer, and raw material supplier levels. Essentially, the farther up the supply chain you go, the more pronounced these demand variations become.
Causes of the Bullwhip Effect:
- Demand Forecasting: When each stage in the supply chain forecasts demand based on orders received, it can amplify demand fluctuations.
- Order Batching: Companies order in large batches to take advantage of economies of scale, leading to spikes in demand.
- Price Fluctuations: Promotions and discounts can cause irregular purchasing patterns.
- Rationing and Shortage Gaming: When customers anticipate shortages, they might order more than needed, causing further distortions.
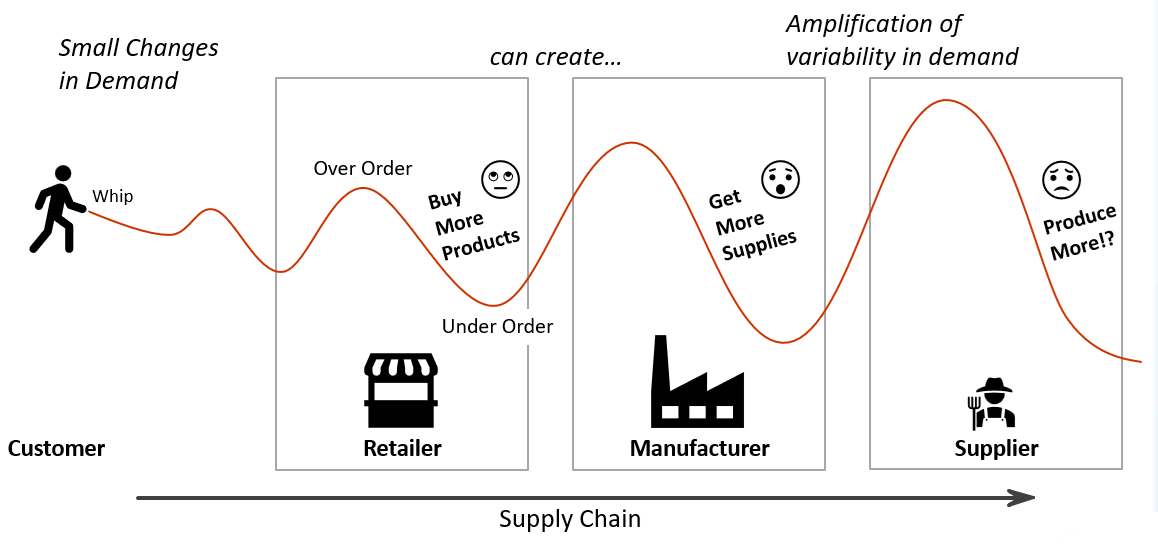
Conclusion
Understanding Supply Chain Management is crucial because it enables businesses to optimize their operations, reduce costs, and improve efficiency. With a clear grasp of SCM principles, companies can ensure a smooth flow of goods and services from suppliers to customers, minimizing delays and disruptions. Effective SCM also enhances customer satisfaction by ensuring timely delivery and quality of products. Additionally, it allows businesses to respond swiftly to market changes and demand fluctuations, maintaining a competitive edge. In essence, mastering SCM is key to building a resilient, agile, and efficient supply chain that drives overall business success and profitability.